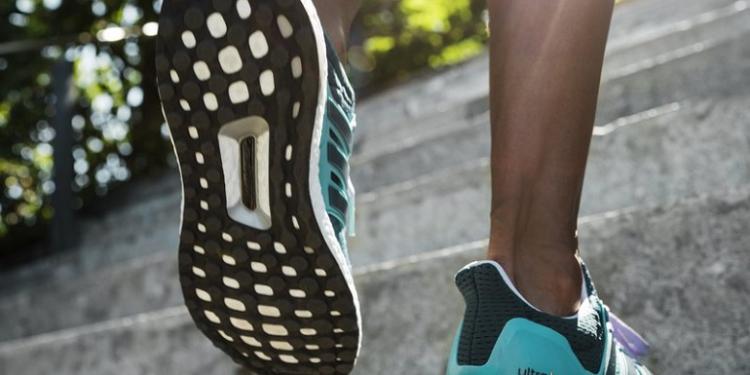
We know you look for grip in your tires, but you also look for grip in your shoes. That’s right, shoes. Continental and adidas have partnered to give you grip on and off the street. Continental and adidas complement one another to perfection in their joint efforts in the field of running shoes and outdoor footwear. In the following interview, the developers at Continental and adidas report on how it all came about and on the long, hard road to production-readiness. See what Fabian Dettmer, Head of Mixing & Process Development at Continental and Gerd Manz, Senior Innovation Director at adidas have to say about the partnership:
Q: How did this cooperation between adidas and Continental come about?
Dettmer: It all began early in 2007 when we met with our counterparts from adidas at a workshop. At the time, adidas were working on a project designed to improve the grip of their shoes. With this aim in mind, Gerd Manz and his colleagues were on the lookout for an expert partner from the rubber industry. So we made a good match.
Manz: That’s right. In the course of the workshop we got to know the team from Continental and we got talking about the similarities between car tires and running soles. That gave rise to the idea. We stayed in touch and started experimenting, initially with a rubber compound for motorcycle tires specifically for use in the wet. But the shoe turned out to have so much grip that you could walk up walls in it – far too much for a shoe, where you also need what’s called “rotational freedom” to prevent injuries.
Dettmer: We were sure that we had the materials to help adidas, after all, here at Continental grip stands for short stopping distances and perfect handling, making it one of the top priorities as we develop materials for our tires. Initial samples that we produced confirmed our view that we could come up with something better than the existing soles. There was a tangible difference.
Q: But why go and develop a whole new shoe when surely everything has already been tried before?
Manz: Expectations of products are forever rising, particularly in the leisure sector. People attach great importance to their leisure time. Everyone’s keen to make the best possible use of it. And in sports that means automatically setting the bar high in terms of your own performance. People are less and less willing to compromise – not even in training, let alone in actual events. And when we turn to the outdoor segment, at times the quality of the equipment can be a matter of life or death. In running, the grip that a shoe provides can mean better performance; on demanding mountain hikes it’s a safety factor.
Dettmer: The exciting thing for us was being able to apply our experience to the field of running shoes. And of course there was the matter of being able to present the Continental brand in a new environment, where we could boost brand awareness in different markets and demonstrate our expertise.
Q: What are the main challenges when you’re developing a running shoe?
Manz: We keep the focus firmly on the customer. It’s often the case that the customer can’t say exactly what makes the decisive difference for them. So we analyze precisely which features make that difference and what the customer likes and doesn’t like. With running shoes, obviously they need to be fast, light and comfortable. Improving these traits is a complex and ongoing process. There are many different expectations to meet. We need to look at the energy management of the shoe as a whole – support, stability, grip... The sole has a key part to play here. Much like the tires in a car, it has to cope with very high loads, perform well at temperatures between minus 20 and plus 40 °C and much more besides.
Q: And what new challenges did the developers at Continental find themselves facing?
Dettmer: We found we were dealing with a whole new set of parameters, starting with the fact that, in contrast to tires, shoe soles are stuck to the uppers with adhesive. Then to avoid placing restrictions on the shoe designers there must be no loss of color in direct contact with white or light-colored midsoles. Also in contrast to tires, indoor shoes must be non-marking, which means they must not leave any traces on the floor. But the fact is that many of these understandable requirements have a direct impact on the composition of the materials used, such as the proportion of black fillers in the compound. We had to work hard to meet the criteria for a constant level of grip in the rubber sole. A tire will normally run on asphalt, concrete or occasionally off-road, but with a shoe we’re also talking about moving safely over tiles, linoleum, grass, moss and wood. That calls for a different set of properties than in a tire.
Q: At what stage and how do you involve athletes in the development process?
Manz: Initially it’s very limited, but as the technology matures we step up the involvement of top-class athletes in testing prototypes. We once provided the former marathon world record holder Haile Gebrselassie with a prototype for test purposes. Imagine our surprise when he decided to run the famous New Year’s Eve race in Trier wearing these shoes. That was in 2009, it had been raining and part of the course was on cobbled streets. Not only that, but the crowds had thrown lots of confetti on the track. So Haile spontaneously decided to wear his test shoes based on material derived from wet-weather motorcycle tires. He won the race by a big margin!
Q: How do you actually test shoes and where does a sole get its grip from?
Dettmer: Interestingly, the contact patch in a shoe is not much smaller than that of a car tire. To see where the grip comes from we have to look at the macroscopic level. How much energy is lost during traction – during the power transmission process? How much energy is converted into heat at this point? In comparative tests we were able to determine that with our compounds we can achieve a 15-30 percent improvement in grip. But it was also important to find out how the materials behave in the various processing steps that are used in shoe manufacturing. We took all of these things into account in our test labs in Hanover.
Manz: The tests that Continental performed and the ones we ran in our own labs complemented one another. What we study here are metrics such as traction on wet and dry surfaces, as well as damping. How does the sole perform on rough, uneven and smooth surfaces? Then there are strict regulations in terms of harmful substances. After all, shoes are items of clothing. All rubber compounds that we use in our models are subjected to rigorous controls in line with our high quality standards.
Q: How long does it take for a running shoe to make it from initial idea to production readiness? And how does that compare with a tire?
Dettmer: The length of the tire development process can vary strongly. It depends on whether we can meet the requirements in terms of dynamic handling and control with established technologies or if we need to apply whole new approaches to make a substantial improvement in properties such as stopping distance, rolling resistance and mileage. In this latter case, developing a new tire line can easily take two or three years. Along with the tread pattern, the design of the tire is also revised and the materials that go into the components improved and harmonized with one another. But by the time whole new technologies have found their way into a product, as much as three to five years can go by.
Manz: For a standard running shoe it normally takes roughly 18 months to get from idea to production readiness. In this special collaboration, though, we set aside three years from our first encounters to the finished product.
In the meantime, collaboration has matured to such an extent that we have no problem combining the materials from Continental with even the new Boost sole that we developed together with BASF.
Q: It’s not just running shoes with Conti soles that you’re developing but outdoor shoes as well. What are the main differences between running and outdoor models?
Manz: Grip and traction are the key functions in both types of shoe, but while in running shoes the focus is on performance attributes like efficiency and acceleration, in the outdoor sector the spotlight is on protection and safety aspects. In terms of tread design too we’ve been able to adopt quite a few things from tire technology to address the enormous demands on performance and robustness in dynamic outdoor sports such as trekking and hiking.
Dettmer: When it came to tread concepts our experience in the mountain bike sector came in useful. While you can’t simply transfer an MTB tire tread 1:1, there are certain similarities in the way geometric structures behave in rough terrain and in how to use tread blocks for specific applications. But we also have to consider the visual appeal of the shoes, because runners and trekkers also have their own expectations of the way their shoes will look – and of course we need to meet those expectations.